อยากรู้ไหมว่ากว่าจะเป็นสมาร์ทโฟนที่เราใช้กันอยู่นี้ มีกระบวนการผลิต และหน้าตาเครื่องผลิตเป็นอย่างไรบ้าง วันนี้เราจะขอแบไต๋ความรู้นี้ หลังทีมงานเว็บแบไต๋ได้ไปด้อมๆ มองๆ สายการผลิต Huawei P10 ที่โรงงานในเมืองตงก่วน (Dongguan) ประเทศจีน ก็ต้องขอบคุณทาง บริษัท Huawei Consumer Business Group (ประเทศไทย) สำหรับทริปส่องโรงงานในครั้งนี้ครับ!
โรงงานผลิตของหัวเว่ยในเมืองตงก่วนนั้นมีพื้นที่ประมาณ 39,000 ตารางเมตรนะครับ โดยมีสายการผลิตแบบ SMT (Surface-mount technology) 18 สายการผลิต และสายการประกอบผลิตภัณฑ์อีก 31 สาย หนึ่งสายการผลิตก็ประกอบมือถือได้ประมาณ 2,000 เครื่องต่อวัน โรงงานนี้จึงผลิตสมาร์ทโฟนได้ราว 1.3 ล้านเครื่องต่อเดือน และอุปกรณ์ใช้ในบ้านอีกราว 300,000 ชิ้นต่อเดือน
สายการผลิตสมาร์ทโฟนของหัวเว่ย
โรงงานประกอบในเมืองตงก่วนนี้ไม่ได้ผลิตชิ้นส่วนในสมาร์ทโฟนเองนะครับ แต่ชิ้นส่วนเกือบทุกอย่างในสมาร์ทโฟน 1 เครื่องนั้นจะมีบริษัทรับผลิตขึ้นมา เช่นชิป Kirin 960 หัวใจของ Huawei P10 แม้ว่าจะออกแบบโดย HiSilicon บริษัทลูกของหัวเว่ยที่ดูแลงานออกแบบชิปประมวลผล แต่ก็ผลิตโดยบริษัท TSMC (Taiwan Semiconductor Manufacturing Company) จากไต้หวันที่เชี่ยวชาญเรื่องการผลิตชิปมากกว่า โดยสมาร์ทโฟน 1 เครื่องนั้นใช้ชิ้นส่วนประมาณ 3,000 – 5,000 ชิ้นครับ
- โลกนี้มีบริษัทผลิตมือถือแค่ 3 รายในโลกที่ออกแบบซีพียูใช้เองคือ Huawei, Samsung และ Apple
- และโลกนี้ก็มีบริษัทผลิตชิปยักษ์ใหญ่แค่ 3 รายคือ Intel, Samsung และ TSMC โดย 2 รายหลังจะรับงานผลิตตามแบบจากบริษัทอื่นๆ ด้วย ส่วน Intel นี่นานๆ ที
สายการผลิตสมาร์ทโฟนของหัวเว่ยแต่ละสายนั้นยาวประมาณ 150 เมตร โดยจะมีทีมงานควบคุม 26 คนต่อสายการผลิต ซึ่งด้านหน้าของแต่ละสายการผลิตก็จะมีหน้าจอบอกว่าสายผลิตนี้กำลังผลิตเครื่องในรหัสอะไร (ซึ่งไม่ใช่รุ่นผลิตภัณฑ์อย่าง P10, Mate 10 ที่เราคุ้นเคย แต่เป็นชื่อภายในของบริษัท) มีวิศวกรดูแลเป็นใครบ้าง และผลการผลิตจนถึงปัจจุบันว่าผลิตไปได้แล้วกี่เครื่อง เสียหายกี่เครื่อง และวันนี้ตั้งเป้าจะผลิตได้กี่เครื่อง ซึ่งปกติเป้าการผลิตก็จะอยู่ราวๆ 2,000 เครื่องต่อวันต่อหนึ่งสายการผลิตครับ
โรงงานนี้มีระบบรักษาความปลอดภัยที่แน่นหนามาก โลหะทุกอย่างถูกห้ามนำเข้าโรงงาน สมาร์ทโฟนจะถูกเก็บลงกล่องก่อนเข้าพื้นที่โรงงาน ทีมงานเว็บแบไต๋ก็เป็นนักข่าวยุคจดลงสมาร์ทโฟน พอไปถึงโรงงานเลยงานเข้าเพราะไม่มีสมาร์ทโฟน และกระดาษปากกาติดตัวไว้จดข้อมูลเลย ก็เลยต้องจำข้อมูลเอา ส่วนภาพประกอบต่างๆ ได้รับการอนุเคราะห์จากหัวเว่ยครับ (จะเห็นว่าข้อมูลสำคัญถูกเซนเซอร์ไปหมดแล้ว)
กระบวนการประกอบสมาร์ทโฟนของ Huawei
กระบวนการผลิตสมาร์ทโฟน 1 เครื่องนั้น จุดที่เป็นส่วนผลิตและประกอบจริงๆ มีไม่เยอะเท่ากับส่วนที่เป็นการทดสอบผลิตภัณฑ์ในจุดต่างๆ ว่าประกอบออกมาแล้วใช้งานได้ไม่มีปัญหา โดยลำดับการประกอบมีคร่าวๆ ดังนี้
(1) กระบวนการวาดแผงวงจรด้วยแสง เครื่องจักรจะทำเส้นวงจรต่างๆ ลงบนแผ่นที่เรียกว่า PCB หรือ Printed Circuit Board
(2) เข้าเครื่องตรวจสอบแผ่นวงจรที่วาดออกมากับภาพต้นแบบเพื่อยืนยันว่าลายตรงกัน
(3) เอาส่วนประกอบอื่นๆ เช่นตัวต้านทาน ชิป และอุปกรณ์เล็กๆ เข้าไปติดบนบอร์ด ซึ่งจุดนี้เองที่เรียกว่า SMT (Surface-mount Technology) คือการเอาชิ้นส่วนที่อยู่บนสายเทปไปติดบนบอร์ดเลย ไม่ได้เจาะรูบอร์ดแล้วบัดกรีเหมือนที่เราทำเล่นในโรงเรียน (Through-hole Technology)
(4) ติดกาวเคลือบชิ้นส่วนไม่ให้หลุดออกมา เอาบอร์ดไปผ่านความร้อน และตรวจสอบว่าชิ้นส่วนต่างๆ ติดตรงกับที่ออกแบบไว้ มาถึงตรงนี้จะเรียกว่า PCA หรือ Printed Circuit Assembly หรือบอร์ดที่ประกอบอุปกรณ์แล้ว
(5) ทดสอบสารพัดแบบว่าบอร์ดที่ผลิตออกมาตอนนี้สามารถทำงานได้ในสภาพแวดล้อมที่เหมือนการใช้งานจริง
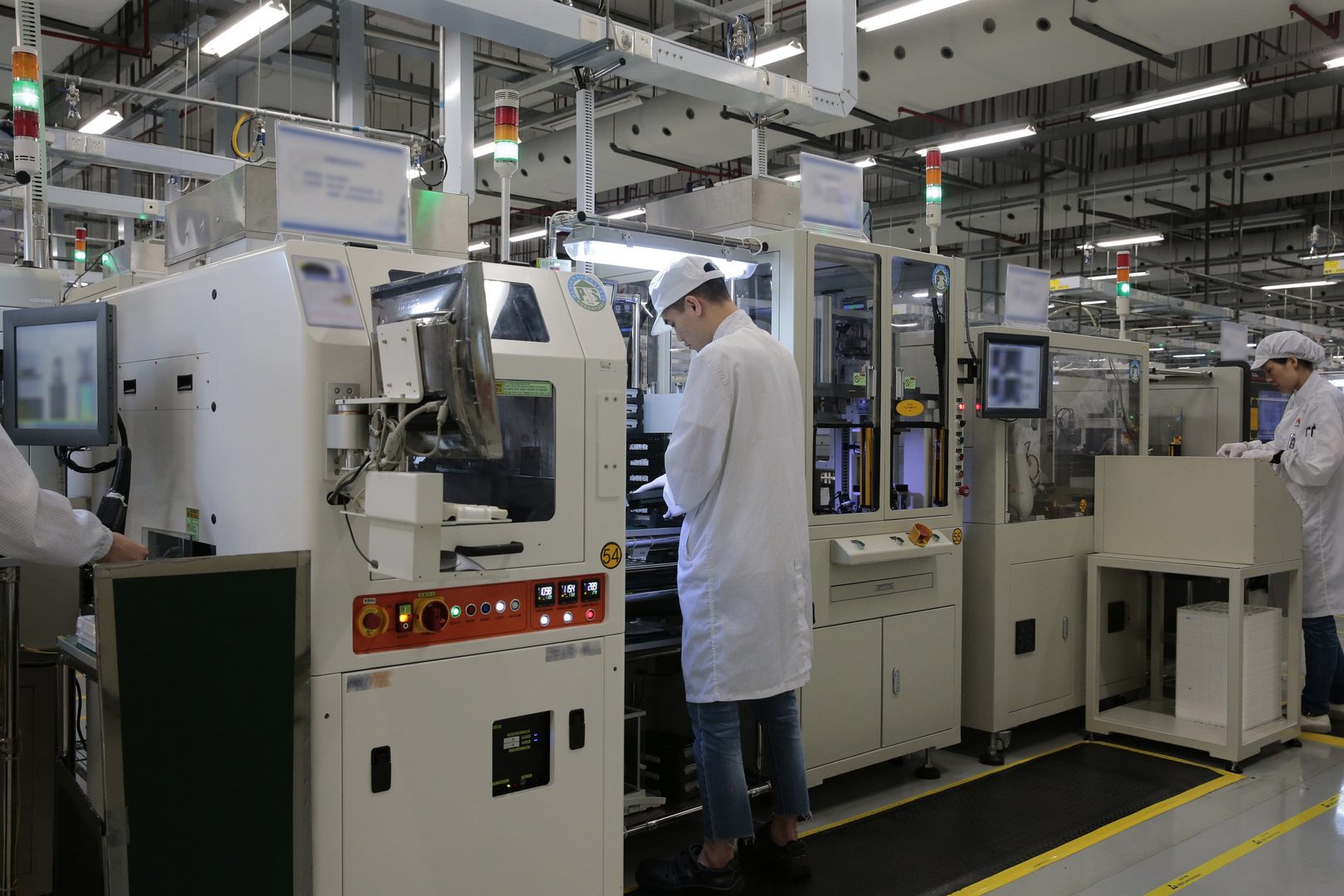
แม้ว่าสายการผลิตส่วนใหญ่จะทำด้วยระบบอัตโนมัติ แต่บางจุดเช่นการประกอบกล้อง-แบต และการเทสบางอย่างก็ยังต้องใช้คนอยู่
(6) นำบอร์ดไปประกอบกับกล้อง ประกอบแบตเตอรี่ 2 ขั้นตอนนี้ยังต้องใช้คนเพราะมีชิ้นส่วนมีความบอบบาง พอประกอบเสร็จก็เทสกล้องว่าได้ภาพตัวอย่างอย่างที่ต้องการ เทสแบตให้ผ่านมาตรฐานความปลอดภัยพื้นฐาน
(7) เทสอุปกรณ์ทุกส่วน ตั้งแต่ตัวบอร์ดเดียว เครื่องที่ประกอบกับแบตเตอรี่ จอ โดยเอาจอเปล่าๆ มาเสียบเทสก่อน ประกอบเสร็จก็เทสอีกที เทสเสียง เทสต่อเนื่อง 3 ชั่วโมงแบบใช้จริงที่อุณหภูมิ 30 องศา
(8) พอทดสอบจนผ่านว่าเป็นอุปกรณ์ที่ใช้ได้จริงๆ จะอัปโหลด firmware ลงเครื่อง ตอก IMEI และ Serial เครื่องเพื่อทำฐานข้อมูลเครื่องจำหน่าย และเทสระบบซอฟต์แวร์อีกครั้ง
(9) สุดท้ายคือนำเครื่องที่ประกอบเสร็จลงกล่องมือถือ และจัดชุด 10 กล่องมือถือเพื่อเอาไปลงกล่องใหญ่ เก็บเข้าโกดังต่อไป
โดยเครื่องจักรที่ใช้ในการประกอบนี้มาทั้งจากอเมริกา ญี่ปุ่น เยอรมัน สวิสเซอร์แลนด์ และก็มีเครื่องเทสอุปกรณ์ที่หัวเว่ยออกแบบเองด้วย
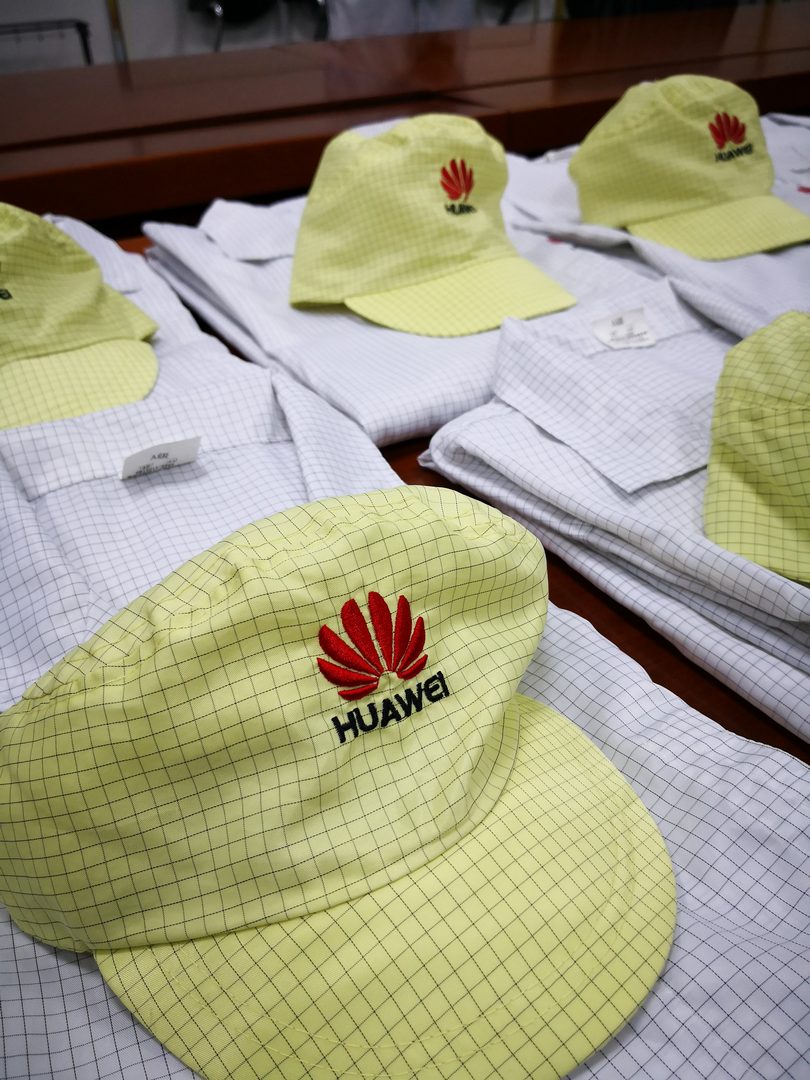
ฝากหมวกหัวเว่ยไว้ให้คิดถึงโรงงานที่ระบบรักษาความปลอดภัยแน่นหนา ห้ามเอาโลหะเข้าไปเลย สมาร์ทโฟนถูกเก็บไว้ในกล่องด้านนอกหมด
ก็จบทัวร์โรงงานนะครับ เดี๋ยวบทความต่อๆ ไป เราจะพาไปดูห้องทดสอบผลิตภัณฑ์ก่อนผลิตจริง ทดสอบกันหลายอย่างกว่าจะไฟนอลเป็นแบบจริง และอนาคตก้ับโลก IoT ของหัวเว่ยครับ